AVISTA Food safety: Case StudIES

Implementing Proven Food Safety Practices
The following case studies are the results of many years of research in the food safety field. These real-life examples demonstrate the best practices in action that prevent recalls, mitigate risk factors, and reinforce our client’s brand and reputation.
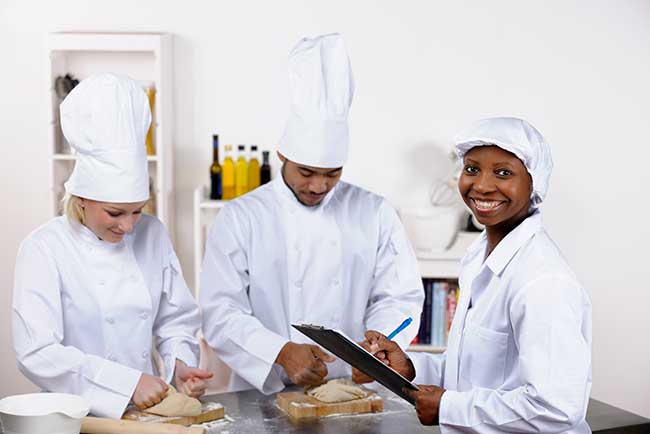